Based on pertinent regulations and standards like NFPA 13, NFPA 25, and NFPA 14, this blog post answers 12 often-asked questions (FAQs) about fire prevention systems, therefore offering insights and direction. Important subjects addressed are hydrostatic testing, fire pump testing, fire department connections, waste chute sprinkler needs, miscellaneous storage allowances, trapeze hanger load capacity, CMSA sprinkler exceptions, mixing sprinkler coverage styles, residential sprinkler requirements, sidewall sprinkler placement, deluge system adjustments, and conveyor sprinkler requirements. By offering clear, succinct responses to often-asked issues and guaranteeing adherence to pertinent fire safety rules, the blog seeks to help building owners, code officials, and fire protection professionals.
#1. Underground Fire Main—Hydrostatic Testing Description- The question is about whether it is acceptable to cover subsurface pipe joints during hydrostatic testing, which is used to assess the piping system's integrity and pressure-holding capabilities. The contractor recommends covering the pipes and all junctions prior to the test and requesting that the fire marshal sign off, accepting responsibility for any joint failures under pressure. The investigation seeks to determine whether this practice is consistent with applicable codes, such as NFPA 24, which typically require joints to be exposed during testing to detect potential leaks or failures, and whether it is prudent to accept this approach given the potential risks and code compliance issues. Question 1. Can subterranean piping joints be covered during hydrostatic testing? The contractor requests that the fire marshal sign off, indicating that they are accountable for any joint breaks under pressure. The contractor plans to cover the pipe and all junctions for the hydrostatic test. Should we tolerate it?
Yes, fittings for the subsurface service can be covered while hydrostatic testing. However, this practice warrants more consideration.
Hydrostatic testing involves leaving joints open to detect leaks and repair them quickly. Section 10.10.2.2.4 of the 2019 edition of NFPA 24 requires that the trench be backfilled “between joints.” To discover leaks during the hydrostatic test, fittings should be left uncovered.
Section 10.10.2.2.6 allows for joint covering “where required for safety” due to the risks associated with uncovered trenches.
If joints are covered during hydrostatic testing, the contractor is responsible for identifying and repairing leaks. This obligation is defined in A10.10.2.2.2.4 and Section 10.10.2.2.5.
The NFSA and EOD procedures do not determine whether AHJs need cover joints during hydrostatic testing. The purpose is to clarify the criteria of the standard. According to NFPA 24, joints may be covered for safety reasons. However, all hydrostatic test procedures, including the allowances outlined in Section 10.10.2.2.6, must be followed.
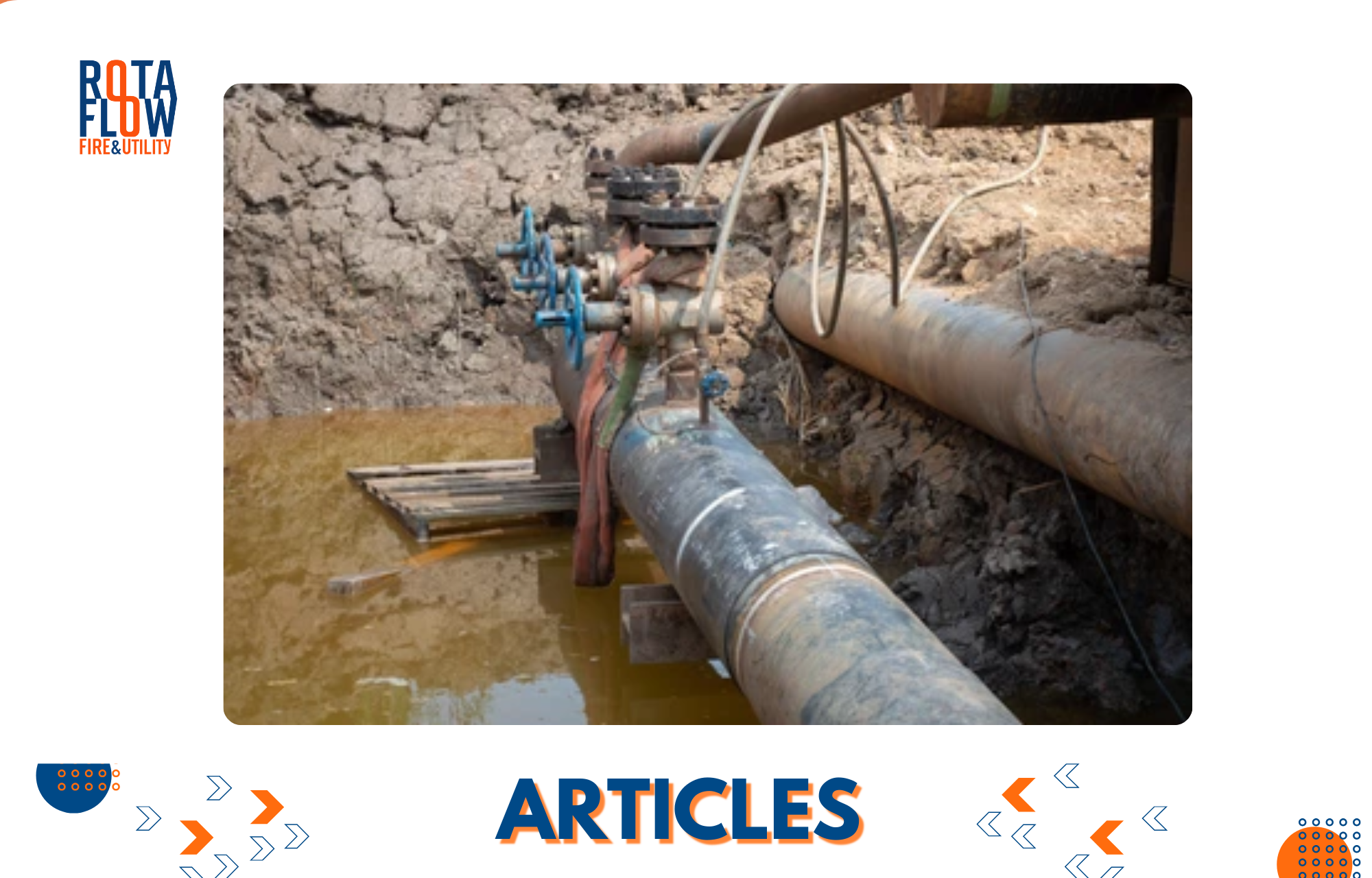
#2. Fire Pump Test Evaluation Description- The question asks how to comply with NFPA 25 (2017 edition), Section 8.3.7.2.3(1), which involves determining the ``full system demand`` for fire pumps that only serve pipe-schedule systems. The term ``full system demand`` refers to the amount of water flow and pressure needed to meet the fire protection system's operational requirements during a fire. Question 2. NFPA 25 (2017 edition), Section 8.3.7.2.3 (1) requires determining ``full system demand`` for fire pumps that only serve pipe-schedule systems. How can this be accomplished?
Ans. NFPA 13 stipulates minimum water flow rates at the base of the riser but only requires minimum residual pressure at the highest sprinkler level.
You have found a substantial challenge with NFPA 25 (2017), Section 8.3.7.2.3(1), especially for pipe-schedule systems with little performance data at the base of the riser.
In pipe-schedule sprinkler systems, NFPA 13 requires minimum flow rates and residual pressure at the highest sprinkler. However, it does not specify the required residual pressure at the riser’s base. The fire pump’s performance cannot be directly compared to the entire system demand, unlike in hydraulically calculated systems.
To estimate system demand, utilise the minimum flow rates listed in NFPA 13 for the appropriate pipe sizes. The flow rate indicates the system’s volume requirements during peak demand.
NFPA 13 requires a minimum residual pressure at the highest sprinkler, which may be calculated backward by accounting for system height and friction loss to estimate the minimum pressure needed at the riser’s base. This approach gives a good reference for determining whether the pump’s output can sustain the requisite pressure and flow rates, while it is not precise.
To account for elevation gain (0.433 psi/ft), an existing ordinary hazard pipe-scheduled system with a minimum residual pressure of 20 psi at the highest sprinkler located 40 feet above the fire pump discharge would need a residual pressure of approximately 37.3 psi at the discharge point.
#3. Fire Department Connection Pipe Size Description- Using the 2016 edition of NFPA 14, a standpipe project requires two FDCs with two 2-1/2 inch outlets each to meet the requisite four outlets. Question 3. What size of pipe is required to feed each FDC? Does each FDC need to provide 1,000 GPM?
Ans. The standard does not specify the pipe size for fire department connections (FDCs), but it should be sufficient to provide at least 500 GPM from both FDCs. If the building is completely sprinklered by NFPA 13, a 4-inch pipe is the minimal size necessary.
FDC inlets are sized based on standpipe system demand, with 250 GPM allocated for each 2-1/2-inch inlet and up to 1,000 GPM for fully sprinklered buildings covered by NFPA 13. Multiple FDCs can be used to accommodate system demand, but each connection must have at least two 2-1/2-inch inlets (Section 7.12.3.2).
Section 7.6 of the standard describes the minimum pipe size requirements. Section 7.6.1 specifies a minimum pipe size of 4 inches for completely sprinklered buildings and 6 inches for partially sprinklered structures.
The 2024 edition of the standard includes annexe language for high-rise buildings, indicating the need to deliver entire system demand from both FDCs.
According to Annex Section A.10.7.2.2.2 of the 2024 edition of NFPA 14, high-rise buildings that exceed fire department pump capabilities may face challenges in supplying system demand through two separate FDCs. Additionally, fire departments often have varying engine pump capacities, making it difficult to pump both FDCs simultaneously.
- Some buildings may need a single fire department pump to fulfil whole system demand through a single FDC.
- In such circumstances, structures should have two FDCs, each sized to accommodate the full system demand.
#4. Multiple Waste Chutes Description- The viability and legality of employing a single sprinkler system to serve several garbage chutes within a structure, rather than providing each chute with its own sprinkler zone. It asks for clarification on whether fire protection standards and best practices allow for a shared system to cover all chutes or require that each chute be zoned separately. This entails comprehending code requirements, such as those from the NFPA or other local fire safety standards and weighing the practical and safety implications of each option. Question 4. Is it possible to supply several garbage chutes in a building with a single sprinkler system, or does each chute require its own zone?
Ans. According to NFPA 13 and NFPA 82 (Standard on Incinerators and Waste and Linen Handling Systems and Equipment), there is no obligation to “zone” waste chutes.
Multiple trash chutes can be supplied by a single sprinkler system, and no separate “zones” are necessary.
Section 11.2.3.4.1 of NFPA 13 (2013) provides discharge parameters for sprinklers connected to their own riser. If the sprinklers in the trash chute are powered by sprinklers on adjacent levels, hydraulic calculations become more complicated, and Section 11.2.3.4.1 cannot be used. Some prefer a separate riser to simplify calculations.
#5. Maximum Area Allowed for Miscellaneous Storage? Description- The issue is whether it is acceptable to put sprinklers with various temperature ratings—ordinary and intermediate—in the same room or area, as long as no particular heat sources influence the temperature. The risk is that combining different temperature ratings might result in uneven sprinkler activation
Ans. According to NFPA 13, miscellaneous storage cannot exceed 10% of the building area or 4000 square feet of sprinklered area. This phrase appears in both the 2025 and prior editions.
Is this phrase valid, or should it read, “whichever is less”? A small mattress manufacturing plant (20,000 square feet) stores raw and finished polypropylene goods that exceed 2,000 square feet (10 percent of the building) but are less than 4,000 square feet. The designer refers to this as random storage and designs it for exposed/unexpanded groups. Plastics can be stored in multiple-row racks up to 12 feet high, with one set of sprinklers and an OH2 ceiling density.
The guideline should be “whichever is less,” as “whichever is greater” would allow a 10,000 square foot facility to have 4,000 square feet (40%) of “miscellaneous storage.”
NFPA 13, 2016 version, defines miscellaneous storage based on six circumstances.
According to Section 3.9.1.18, miscellaneous storage is incidental to another occupancy use group, does not exceed 12 feet (3.66 m) in height, is not more than 10% of the building area or 4000 ft2 (372 m2) of the sprinklered area, does not exceed 1000 ft2 (93 m2) in one pile or area, and is at least 25 feet (7.62 m) away from other storage areas.
This section defines miscellaneous storage as meeting the following six conditions:
- does not surpass 12 feet (3.66 meters) in height.
- is ancillary to other occupancy use groups.
- Does not exceed 10% of the building area or 4000 ft² (372 m²) of sprinklered space.
- do not surpass 1000 ft² (93 m²) in one pile or area.
- is at least 25 feet (7.62 meters) apart from the other storage locations.
The intention behind item 3 above is to be “whichever is greater.” However, items 4 and 5 still apply.
A 20,000 square foot structure can accommodate up to 4,000 square feet of miscellaneous storage, as long as the storage height does not exceed 12 feet and it is not used for another purpose. Storage areas must be at least 25 feet apart and no larger than 1,000 square feet apiece. You can have up to four miscellaneous storage areas totalling no more than 4,000 square feet. Each area must be less than 1,000 square feet and at least 25 feet apart.
A 10,000-square-foot facility can accommodate up to 4,000 square feet of miscellaneous storage. However, each space cannot exceed 1,000 square feet and must be separated by 25 feet. Some smaller buildings may not be able to meet the additional standards.
#6. Trapeze Hanger Point Load Description- The question looks into the load-bearing capacity of trapeze hangers used in fire protection or plumbing systems. It specifically questions whether these hangers can hold not just the weight of a water-filled pipe, but also an additional 250 pounds, efficiently conveying this combined load between two structural connection sites. This includes evaluating the trapeze hangers' design parameters, material strength, and compliance with relevant regulations, such as those in NFPA 13, to assure safety and structural integrity under the stated conditions.Question 6. Can trapeze hangers transmit the weight of a water-filled pipe, plus an additional 250 pounds, between two structural attachments?
Ans. Using a trapeze hanger does not distribute the weight of the water-filled pipe and an additional 250 pounds between the two structural components.
According to NFPA 13 (2019 edition), two trapeze hangers cannot share the load of a sprinkler pipe.
Key sections of NFPA 13:
- Section 17.1.4.1 addresses shared supports for sprinkler piping and other professions. However, employing a trapeze hook for sprinkler piping does not distribute the load.
- Section 17.3.5 requires all hanger assembly components attached to trapeze members to meet Section 17.1.6 standards and support the hanging sprinkler pipe.
According to the guide commentary, trapeze hangers have three hanging points: the two ends and the suspended load. Each hanging point has two attachment points: top and bottom. According to Subsection 17.3.5, all hanger assemblies and components must be sized to accommodate the total suspended load.
Common Mistakes and Correct Practices:
- Sizing Components for the Maximum Load: All trapeze components should be sized to accommodate the highest load possible.
To support an 8 in. (200 mm) main with a 4 in. (100 mm) trapeze, all components, including rings, rods, and attachments, must be sized for the pipe weight.
- Top attachments (e.g., g-clamps, lag bolts) must fit the 8 in. (200 mm) main and not the 4 in. (100 mm) trapeze.
- Hanger rods must be 1⁄2 in. (13 mm) in diameter for 8 in. (200 mm) pipe loads, not the smaller 3⁄8 in. (10 mm) diameter for 4 in. (100 mm) pipes.
- Rings and Attachments:
Standard 4 in. (100 mm) rings are not designed to support 8 in. (200 mm) pipes. Oversized rings for 8 in. (200 mm) pipes should not be used to hang a 4 in. (100 mm) trapeze due to potential distortion. Manufacturers offer heavy-duty rings or other connections that do not require rings.
Alternative approaches:
- Engineered hangers:
Hangers approved by a qualified professional engineer and meeting all five criteria in Section 17.1.2 are an acceptable alternative to Chapter 17’s standard standards.
- Close Spacing of Hangers:
Use closely spaced hangers instead of trapeze hangers.
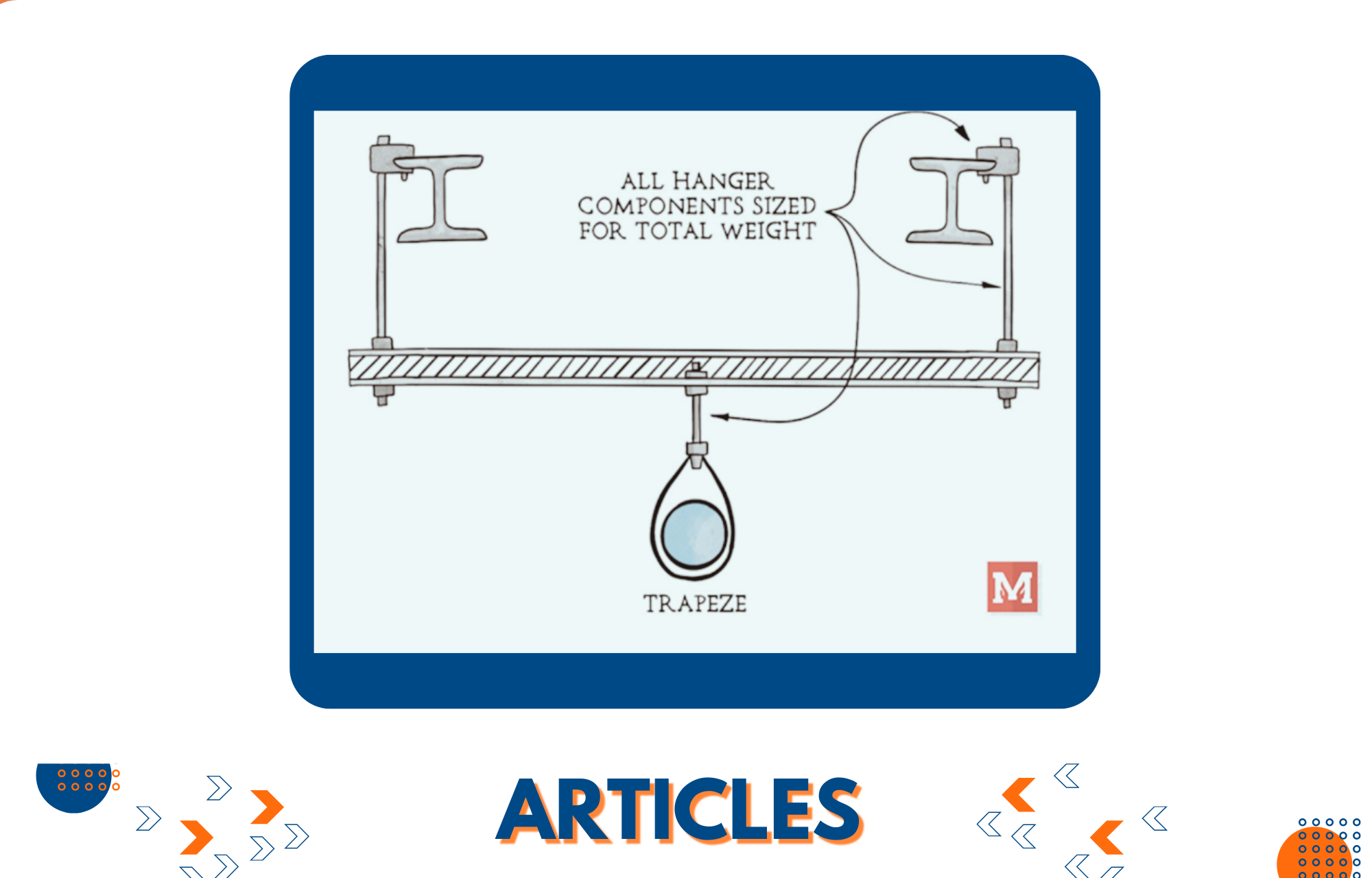
#7. CMSA Smoke/Heat Vent Exception Description- Smoke and heat vents are not required for CMSA or ESFR sprinkler installations, according to IFC 910.2, Exception #3, and the Ohio Building Code (OBC). Exception #3 requires that CMSA sprinklers meet two conditions: 1. A Response Time Index (RTI) of 50 or lower. 2. A listing for fire control or suppression using 12 or fewer sprinklers. Question 7. NFPA 13 (2022), Chapter 22, does not include standards for CMSA sprinkler designs with fewer than 15 units. Is the CMSA sprinkler requirement of 12 sprinklers a mistake or inaccuracy in the code guidelines? Is it an intentional attempt to confine the exception to ESFR sprinklers and exclude other types?
Ans. The 2015 IBC/IFC revision included CMSA sprinklers with fast-response technology and a 12-sprinkler design area, making them comparable.
Performance is comparable to that of ESFR sprinklers. The IBC/IFC allows an exception to smoke and heat venting rules when certain conditions are met, similar to ESFR sprinklers.
However, NFPA 13 does not need specific 12-sprinkler designs for CMSA sprinklers. CMSA sprinkler designs with fewer than 12 sprinklers were included in Chapter 21 of the 2013 edition. The 2015 IBC/IFC, which referenced the 2013 version of NFPA 13, included a provision allowing specially listed sprinklers to meet with IBC/IFC criteria and paving the path for future CMSA sprinkler designs in NFPA 13.
NFPA 13’s 2025 edition does not include 12-sprinkler designs for CMSA sprinklers.
#8. Mixing 'Coverage' Styles Description- The system consists of standard-spray upright sprinklers above the baffle ceiling and extended-coverage (E.C.) sprinklers below the baffles. According to NFPA 13 Section 8.5.5.3.3, sprinklers installed under obstructions must be of the same type as those installed at the ceiling. Question 8. The question at hand is whether the E.C. pendent sprinklers below the baffles should be converted to standard-spray sprinklers to match the ``sprinkler type`` above the baffle barrier.
Ans. Extended coverage sprinklers put below an impediment do not require conversion to normal spray sprinklers above the obstruction.
According to NFPA 13 (2016 edition), sprinklers positioned under obstructions must be of the same type (spray, CMSA, ESFR, residential) as those installed above the ceiling, unless otherwise specified in Section 8.5.5.3.3.1.
- Section 3.6.4 describes several sprinkler kinds.
- Spray sprinklers, as defined in Section 3.6.4.11, are designed to mitigate fire threats across multiple categories.
- According to Section 3.6.4.11.1, a conventional spray sprinkler covers the maximum areas indicated in Sections 8.6 and 8.7.
Section 3.6.4.4 specifies extended coverage sprinklers as those with maximum coverage areas specified in Sections 8.8 and 8.9.
NFPA 13 defines “spray sprinklers” to include both the extended coverage sprinkler below the obstruction and the normal spray sprinkler above. This meets the requirements of Section 8.5.5.3.3. Spray sprinklers are divided into standard (pendent, upright, and sidewall) and extended coverage (pendent, upright, and sidewall) types.
The 2025 edition makes changes to how sprinklers underneath barriers are addressed. These are now known as supplementary sprinklers.
- According to Section 3.3.223.3.6, a supplemental sprinkler is one put below an impediment.
- Sections 9.5.5.3.3 and 9.5.5.3.4 specify standards for additional sprinklers, including positioning and spacing.
The key requirements for additional sprinklers include:
- According to Section 9.5.5.3.3.1, quick-response sprinklers must have a fast-response thermal element and a nominal ordinary temperature rating, unless otherwise specified by Sections 7.2.4 or 9.4.2.5. 2. Supplemental sprinklers must have the same K-factor, orientation, and coverage type as ceiling sprinklers, unless specified in Section 9.5.5.3.3.3.
- 2. Section 9.5.5.3.3.3 allows for different K-factor, orientation, and coverage-type features for supplemental sprinklers that meet Section 19.5 standards.
#9. Closets in Residential Units with Communication Equipment Description- Section 30.3.5.3 of the Florida Fire Prevention Code, which implements NFPA 101, states that closets less than 12 square feet (1.1 m2) are not required to have sprinklers. Sprinklers must be installed in closets with equipment like washers, dryers, furnaces, or water heaters, regardless of size. Question 9. Is it necessary to put a sprinkler in a closet with communication equipment, such as phones, internet boxes or 120V outlets?
Ans. No, sprinklers are not required in this closet. Since 1976, NFPA 101 has exempted sprinklers in small closets in new apartments. NFPA 101 does not define a “closet,” although domestic data/communication equipment supplying the dwelling unit does not come under the types of equipment described in Section 30.3.5.3 (e.g., heating units, electrical motors, or high-amperage equipment). This exemption in NFPA 101 appears to focus on linen and clothing closets, as mentioned in NFPA 13. The inclusion of a data cabinet in an unsprinklered closet under 12 square feet does not considerably raise the fire load in the dwelling unit, necessitating sprinklers.
#10. Sidewall Sprinkler Under Ducts Description- The inquiry investigates the permissibility and feasibility of putting sidewall sprinklers beneath ducts in a building's fire prevention system. It requests clarity on whether this installation is permitted by fire safety codes such as NFPA 13 and whether it would provide appropriate coverage and protection. It also raises concerns regarding potential water distribution obstacles and the influence on the sprinkler system's overall efficacy in preventing or suppressing fires near the ducts. Question 10. Can sidewall sprinklers be put beneath ducts?
Ans. According to Section 10.3.2 of the 2019 version of NFPA 13, sidewall sprinklers can be installed under impediments. Previously, this section focused on their use under overhead doors. In the 2019 edition, NFPA 13 amended this clause to cover additional forms of impediments. The NFPA 13 technical committee explained the modification, stating that sidewall sprinklers are widely employed to defend against blockages and should be explicitly stated in this section. This amendment expands the use of sidewall sprinklers by allowing them to be positioned beneath any impediment that requires sprinkler coverage.
#11. Open-head Foam/Water Deluge Nozzles Description- The query focuses on whether it is possible to increase C1 thermostatic rate-of-rise releases to meet a change in building height, especially a 2-foot-6-inch roof elevation, without raising the deluge system's existing open-head foam/water nozzles. It tries to evaluate if the detection system can continue to function well with the additional height or whether the new configuration will jeopardise the system's ability to detect temperature changes and respond correctly to a fire event. Key concerns include compliance with applicable fire safety rules, such as NFPA 16, as well as the system's design restrictions. Question 11. A customer is lifting an existing building's roof by around 2 feet-6 inches. Can the C1 thermostatic rate-of-rise releases, which trigger the open-head foam/water deluge system, be adjusted to the increased height without raising the existing open-head foam/water nozzles?
Ans. Heat detectors and open foam nozzles must adhere to NFPA 11, NFPA 16, and NFPA 13 requirements for proper positioning. To determine the exact location and distance of nozzles from the ceiling, refer to the listing of the foam nozzles or sprinklers used, as these guidelines may not state it directly. Foam sprinklers and nozzles have minimum and maximum distances from the floor based on the hazard they guard. Adherence to the manufacturer’s listing is essential for proper installation.
In the 2025 edition of NFPA 13, Section 15.1.3 clarifies that when open sprinklers/nozzles are automatically activated by “hydraulic, pneumatic, or other means,” the deflector may exceed the maximum distance below the ceiling indicated in the applicable section for that style of sprinkler.
This clause acknowledges that open sprinklers and nozzles use a distinct detection system (e.g., the C1 thermostatic rate-of-rise release); therefore, their exact location relative to the ceiling is less important for fire detection. According to the NFPA 13 technical committee, open sprinklers and nozzles use a supplemental detection system and may not be affected by their position relative to the ceiling.
Increasing the roof height may not need raising the open foam nozzles, as long as the detecting system (C1 releases) is adjusted and the foam nozzles stay within their installation range.
#12. Conveyor Sprinkler Description- The query requests clarification on the sprinkler requirements for a chain conveyor under the 2022 version of NFPA 13, which now contains rules for floor-mounted conveyors that were lacking in the previous edition. The conveyor in question is nearly four feet wide and three feet above the floor, with no storage beneath it. The inquiry focuses on whether a sprinkler is required for this arrangement, taking into account the new regulations, the conveyor's dimensions, proximity to the floor, and the lack of storage, all of which may influence fire risk and sprinkler installation requirements. Question 12. The 2022 edition of NFPA 13 includes specific standards for floor-mounted conveyors, which were not included in the 2019 edition. Our chain conveyor is almost 4 feet wide but just 3 feet above the floor, with no storage below it. Is a sprinkler required in this scenario?
Ans. It is true that the requirements for minimum temperature ratings and separation distances between sprinklers and radiant tube heaters have not changed with the latest editions of NFPA 13. However, it should be noted that the table (Table 9.4.2.5(a) in the 2019 edition of NFPA 13) that addresses sprinkler temperature ratings based on distance from heat sources now includes an entry titled “unit heater and radiant heater.”
This is a minor modification from the 2016 edition, when the article was only labelled “unit heater” and radiant heaters were not discussed. This makes it clear that the same standards are intended to be used by the NFPA 13 committee.
Courtesy: Roland Asp, CET, TechNotes