ULC Fire Alarm & Gas Detection Solutions
At Rotaflow, we specialize in both fire alarm and gas detection system designs that comply with Canadian codes & standards, ensuring uncompromising safety and reliability. From initial concept to final verification, our expert engineers oversee every stage, delivering solutions tailored to your site’s unique needs.
Our expertise with Autocall and Notifier Fire Alarm Panels, combined with advanced gas detection systems, allows us to design systems that optimize installation, maintenance, and long-term performance.
Our in-house programming ensures seamless functionality, while our engineer-led approach guarantees strict code compliance and peak system efficiency.
Trust Rotaflow to design integrated fire alarm and gas detection systems that protect what matters most without compromise.
Fire Alarm Process:
- Design & Stamping: ULC code-compliant system designs for fire alarms and gas detection systems, stamped for regulatory approval.
- Material Procurement: Sourcing all materials to meet required specifications for both fire alarm and gas detection systems.
- Installation & Verification: Thorough installation and verification processes ensure flawless performance, code compliance, and verification inspection standards.
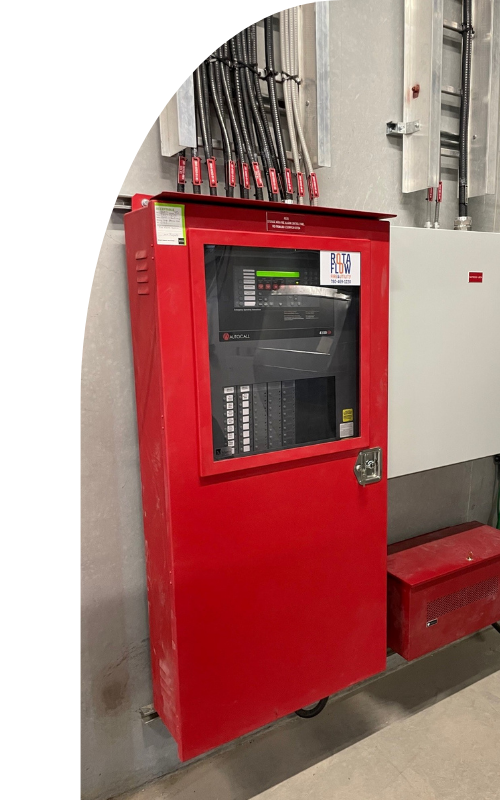
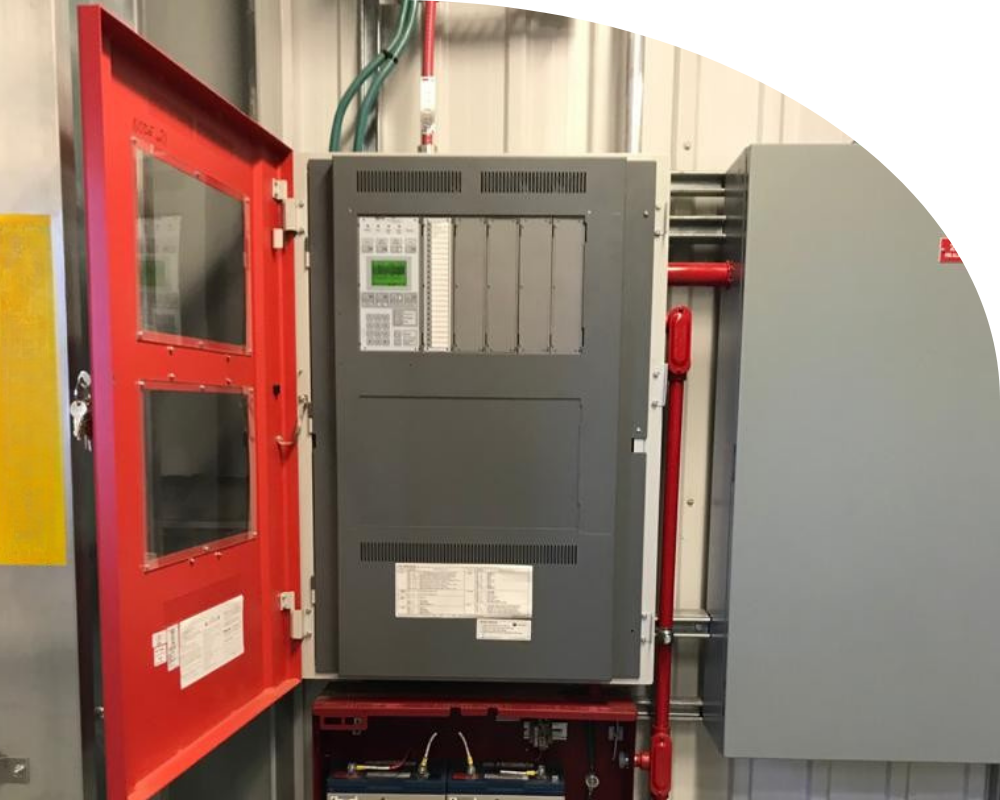
ULC-certified fire alarm service
- Custom Panel Design: Tailored configurations of Autocall or Notifier panels for fire alarm systems, and gas detection panels designed for seamless integration and optimal performance.
- In-house Programming: Full control over customization and performance of your fire alarm and gas detection systems.
- Engineer-Led Process: From design to installation and verification, we lead the process to ensure efficiency, safety, and compliance.
At Rotaflow, we deliver unmatched quality and reliability, focusing on safety and compliance at every stage whether for fire or gas detection.
Advanced Fire Alarm and Gas Detection Services
At Rotaflow, we’re committed to delivering integrated fire alarm and gas detection solutions with the highest standards of safety, reliability, and compliance. Whether you’re installing new systems or maintaining existing ones, we ensure your premises are always protected.
-
- New Construction: Material supply and technician programming.
- Design Build: End-to-end design, procurement, installation, and commissioning.
- Special Hazard Systems: Clean Agent, Pre-Action, Deluge, and Foam systems.
- VESDA: Early warning smoke detection for fire and gas.
- Linear Heat Detection: For conveyors, tanks, cable trays, and more.
- Gas Detection: Customized solutions for hazardous gases.
- Preventative Maintenance: Regular inspections for fire alarm and gas systems.
- Integrated Testing: Certified ULC-S1001 inspections.
- Service: Repairs, troubleshooting, and calibration.
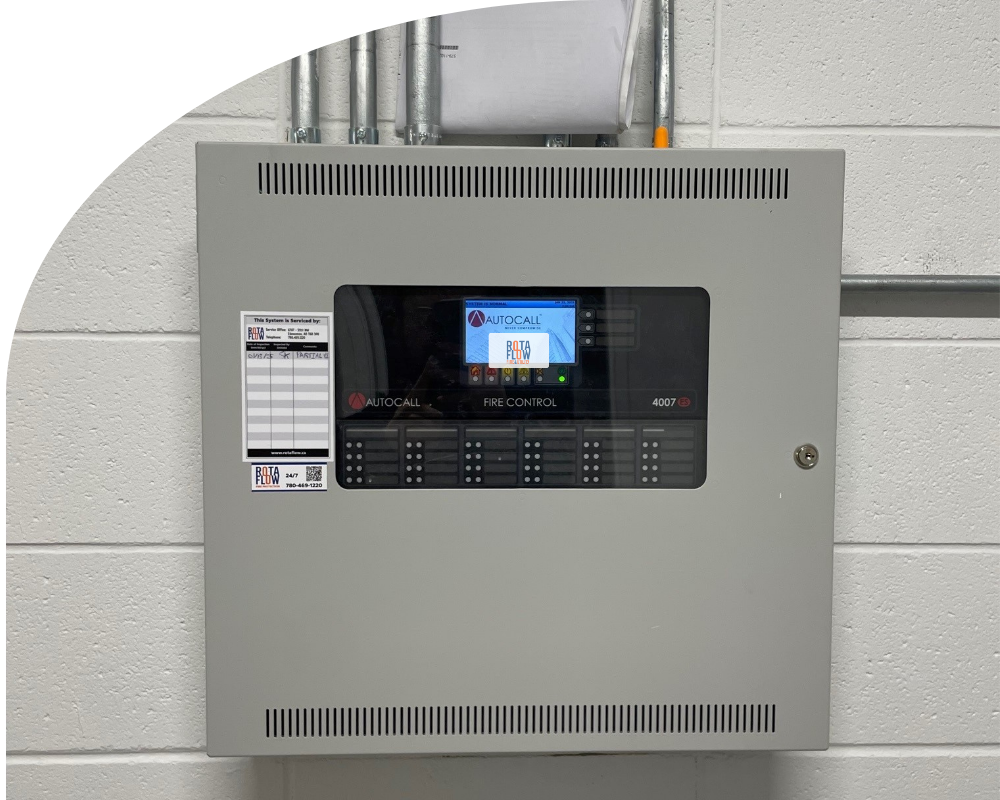
Get a quote today ! Fire alarm inspection and maintenance.
Contact Us
Please note that all forms and emails will be replied to within 24 hours. For immediate assistance, call 780-469-1220.
FAQ
FIRE PROTECTION SIMPLIFIED REQUIREMENTS
As per the new 2019 Alberta Fire Code, Water-Based Fire Protection Systems have to be maintained in good working order and be checked and tested according to NFPA 25. Fire protection systems that are water-based include standpipes, sprinkler systems, public and private hydrants, systems of hoses stationary water sprayers and foam-water sprinkler systems as well as fire pump systems. This standard specifies the minimum requirements. However, higher standards might be demanded by your insurance provider depending on the nature of facility.
Quarterly
A brief inspection is required every three months for certain parts of the system such as Pressure Gauges Water-flow Devices and supervisory Devices. While it is required under the Fire Code, this is not always implemented locally by authorities. But, an investigation after the incident usually requires the reports of the inspections. Failure to perform the quarterly inspections can result in the liability of the company in the event of the system failing.
Yearly
Each year, all the components of the system have to be tested and inspected. Alongside the items that are checked every quarter, it also includes a visual inspection of the entire system from below which means having access across the whole space within the structure is necessary. Also, it is necessary to check all fittings, gauges, drains, valves, and antifreeze as well as fire department hookups wrenches, spare heads, as well as data plates. Also, the Backflow Preventor device should also be examined in conjunction with the Backflow Preventor device in accordance with the requirements of Water Utilities (EPCOR). Based on the complexity and size of your system this could take anything between an hour and several days. The majority of commercial structures are completed in a time of a day. Residential buildings of large size could take a couple of days when you need to gain access to a large number of suites. Industrial sites could take longer. The majority of annual commercial inspections will need only one technician. As every system is different, the best way to obtain an estimate for the cost of an inspection is to provide us with a previous inspection report, along with the size (sq ft) of the building and approximate allocation of space (office/warehouse/shop/apartments/etc).
Non-Annual
Alongside the regular annual maintenance and inspection, additional work could be required on a 3- or 5-year basis based on the kind of system. This may include hydro-static tests, flow-test pressure tests, as well as obstruction investigations. The majority of these tasks are performed by two techs and will take at least a half day.
WHAT DO YOU CAN EXPECT?
Inspections every quarter and annually are usually conducted by a single technician. Technicians will divide the time in between checking the system components in the valve room, and then conducting a visual inspection of the heads and piping throughout the area of protection. This will include checking the connection to your Fire Alarm panel (if connected) and the customer must call their alarm monitoring company to inform them of the test.
If there are any issues in the system, there are two possibilities for what can occur. Minor issues may be addressed by the technician before he leaves When the fix involves the use of any components or labor the client representative should be present to sign off on the work. If the issue is not fixed immediately, it will be reported on the inspection report and a quotation will be given in the event that it is feasible and a follow-up maintenance schedule will be set after approval. Any serious issue with the system will be brought to the attention of our on-site contact.
PREPARATION
There are some things clients must consider in preparation in advance for a visit.
Notice to post – when in a residence, each tenant must be informed at least 48 hours prior to when an inspection is scheduled to take place. Access is required to any unit that has a sprinkler head within.
Monitoring – The majority of systems for alarms are monitored through a company or another monitoring company. The function of a monitoring company is to inform the fire department when an alarm triggers within your system. A part of testing the sprinkler system involves testing for the proper communication to the Fire Alarm panel. In the course of tests, the monitoring company is required to be informed to ensure they don’t initiate an emergency response from the fire department. The customer will have to inform their monitoring provider prior to starting and following the conclusion of the testing.
Access – Technicians need access to every part of the building that has sprinkler protection. This includes server rooms, mechanical rooms as well as residential rooms. Make sure that technicians have keys or escorts when needed.
SOMETHING IS WRONG, WHAT SHOULD I DO?
Don’t panic.
Freeze UPS
Do not freeze the pipes. Turn off your fire alarm (if there is one). Contact us, and let our technician take an initial look. In many instances, it’s much quicker and more efficient to finish repair work in the event that the melt is conducted in a controlled fashion.
It is necessary to set fire watches in the area shut down until the service is restored.
Note that any weekend or after-hours service or moment we have to cancel any other scheduled work in order to send someone out to your premises is deemed an emergency call-out and the minimum charges or overtime rates will apply.
Is the fire alarm and sprinkler system a great combination?
Automatic sprinkler systems and fire alarms have long been used together to protect building inhabitants and improve fire prevention. A fire alarm system is defined by the International Fire Code (IFC) as a system or portion of a combination system consisting of components and circuits arranged to monitor and annunciate the status of fire alarm or supervisory signal-initiating devices and to initiate the appropriate response to the signals. Alarm starting devices and supervisory devices are among the parts that a fire alarm system keeps an eye on. If a monitored alarm device detects a probable fire condition, the fire alarm control panel (FACP) will detect a signal and initiate the proper reaction. If the building has an occupant alerting system, the horn/strobes or voice evacuation system will activate.