Using National Fire Protection Association (NFPA) guidelines, this collection of FAQs explores the complex realm of fire protection engineering. We investigate useful applications of NFPA 13 and NFPA 25, from high-ceiling light danger occupancies to the nuances of auxiliary dry systems and “birdcage” system designs. We discuss typical difficulties that fire safety experts encounter: figuring out wire sizes, making sure sprinklers are placed correctly in unusual architectural settings, and negotiating the complexity of water spray system inspections.
We also look at how FM Global shapes fire suppression rules and go over technical issues with suction pipe sizing in fire pump systems. By tackling these several issues, this blog hopes to provide clarity and direction on important elements of fire safety, therefore illuminating both accepted wisdom and the justification for it. Whether you are a newbie to the industry or a seasoned engineer, these FAQs provide a great tool for grasping and using sensible fire safety measures.
#1. Light Hazard High Ceiling Design Criteria
Description: The sprinkler system is designed for light hazard occupancy with a ceiling height of 45 feet. NFPA 13, 2025 edition, Section 19.2.3.2.5, does not include design standards for light hazard occupancies.
Question 1. Can light hazard occupancies with ceiling heights more than 30 feet be shielded utilising the standard density/area criteria described in Table 19.2.3.1.1?
Ans. There are no limits for light hazard occupancies with ceiling heights over 30 feet. Table 19.2.3.1.1 provides the conventional density/area requirements for design purposes.
The 2025 edition of NFPA 13 introduces high-ceiling advice for ordinary hazard occupancies and higher. This adjustment had no effect on occupancies with light hazards.
The table below summarises the updates:
Ceiling Height – Over 30 ft: Sprinkler Density/Area
Occupancy Hazard | Ceiling Height | Sprinkler Orientation | Sprinkler Coverage | K-Factor | Minimum Density | Increase of Design Area |
OH-1 | >30 ft | Upright & Pendant | Standard or Extended | 5.6 or greater | Per Table 19.2.3.1.1 | 30 % |
OH-2 | > 30 ft but </=40 ft | Upright & Pendant | Standard or Extended | 11.2 or greater | 0.37 | None |
OH-2 | >40 ft | Upright & Pendant | Standard or Extended | 11.2 or greater | 0.45 | 30% |
OH-2 | >40 ft | Upright & Pendant | Extended | 25.2 or greater | 0.45 | None |
EH-1 & EH-2 | >30 ft | Upright & Pendant | Standard | 11.2 or greater | 0.45 | None |
EH-1 & EH-2 | >30 ft | Upright & Pendant | Extended | Greater than 22.4 | 0.45 | None |
#2. Auxiliary Dry System
Question 2. Can a tail-end dry system be installed on an existing wet system according to the 2019 edition of NFPA 13?
Ans. A wet pipe system can feed an auxiliary dry pipe system, if the water supply is sufficient.
Section 8.1.3 of the 2019 version of NFPA 13 outlines this notion. The online version of NFPA 13 (NFPA Link) has “enhanced content,” including a diagram (Exhibit 8.3) depicting a combined riser where the water supply for the dry system comes from the wet pipe system. The illustration shows the auxiliary dry pipe system branching out at the wet pipe riser, but the supply connection can be established anywhere downstream of the wet system control assembly.
Furthermore, the following considerations must be made:
- Section 4.4 specifies the overall system protection area limitations, which include both wet and dry pipe systems. The combined floor area of both systems is approximately 34,000 square feet, meeting the criteria.
- Additionally, the “enhanced content” suggests adding a control valve on the auxiliary system for easier maintenance and resetting.
#3. “Bird Cage” System
Description: The building’s footprint is 28,500 square feet per floor, within the 52,000 square foot limit.
Question 3. Is it uncommon to construct a fire protection system in a four-storey apartment building with shared walls that uses 1-inch vertical feed mains from the first to fourth floors?
Each floor is a perfect duplicate of the others. Is it better to use a floor-controlled system with individual zones, flow switches, and other controls?
Ans. In multi-storey buildings with identical footprints, it was usual practice to install vertical branch lines inside the walls, often known as a “birdcage system.”
Previously, model building and fire codes, as well as sprinkler standards, allowed for this plumbing configuration in non-high-rise buildings. This inquiry refers to the 2010 edition of NFPA 13R, which does not need floor control valves. Recent editions of NFPA 13R require a control valve for fire sprinkler systems fed via standpipe risers.
The relevant NFPA 13R requirements include:
- According to NFPA 13R (2016 edition), if a building has a fire alarm system, the sprinkler system does not need to be zoned by floor.
- Section 6.8.8 of NFPA 13R (2019, 2022, 2025 editions) states that a control valve per floor is not necessary in multistorey buildings.
- According to NFPA 13R (2019, 2022, 2025 editions), each connection from a combined standpipe to a sprinkler system or floor requires an independent control valve and check valve. This setup limits the usage of “birdcage” systems.
- NFPA 13R (2019, 2022, 2025 editions) – Section 6.16.4 states that if a building fire alarm system is present, the fire sprinkler system is not required to be zoned by floor.
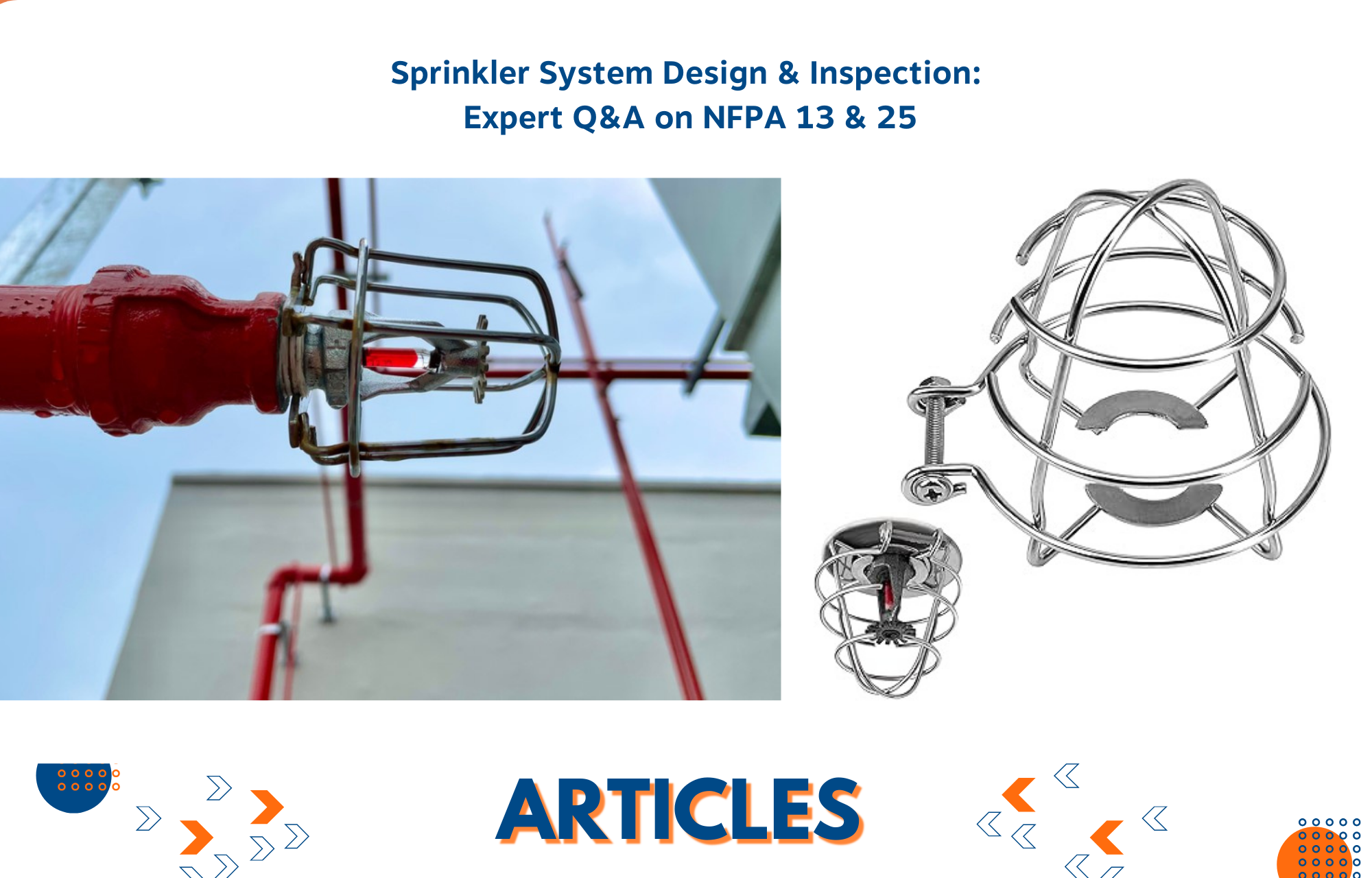
#4. Do Sprinkler Drains Require Riser Clamps at the Top and Bottom of a Floor?
Description: The building features an eight-storey hybrid standpipe and wet sprinkler system. Riser clamps are to be installed on alternate floors below and above the slab, with consideration for drain risers requiring a clamp below the floor.
Question 4. The building contains an eight-storey hybrid standpipe and wet sprinkler system. The request is to place riser clamps on alternate floors below and above the slab. Should drain risers include a clamp below the floor?
Ans. NFPA 13, 2016 edition, Section 3.5.10 defines a ‘riser’ as the vertical supply pipes in a sprinkler system. Risers supply water to system pipes, such as cross mains, feed mains, and branch lines. A drain connection does not feed water to the system; hence, the criteria of Section 9.2.5.4 do not apply.
However, this request is about an eight-storey skyscraper. To support the drain piping, it’s important to consider the building’s height and weight. However, it’s not necessary to provide support at every level, as riser piping is. This support is especially critical for buildings with fire pumps, as opening drains can cause higher-than-normal pressures and water flow.
#5. Water Spray System Inspection
Description: A visual check can confirm whether rubber-gasketed fittings are adequately shielded from water spray. This ensures protection without discharging the system or affecting neighbouring systems.
Question 5. How can a visual check, without discharging the system(s), ensure that all rubber-gasketed fittings are sufficiently protected from water spray from the system or neighbouring system?
Ans. NFPA 25 does not normally require inspectors to refer to as-built or installation drawings during inspections, except for crucial verification purposes. Water spray fixed systems require a nozzle alignment check to assure proper operation.
According to Section 1.1.3, inspectors must assume the system was installed using commonly accepted techniques. This assumes proper design and installation, including nozzle coverage for gasketed fittings exposed to heat.
A water spray fixed system is normally controlled by a deluge valve. Chapter 13 of NFPA 25 outlines the inspection, testing, and maintenance requirements for this valve.
The deluge valve must be tested for full flow on an annual basis. During this test, the technician confirms that all rubber-gasketed fittings are heat-resistant.
The yearly full-flow test assures the appropriate operation of the deluge valve and the effectiveness of protection measures, such as nozzle covering on gasketed fittings.
#6. Is a Sprinkler Required in a Heat Pump Closet in a Condo?
Description: A sprinkler requirement for a heat pump closet in a high-rise condo depends on fire code regulations. The closet is within a housing unit with restricted access, requiring evaluation for compliance.
Question 6. Please advise if a sprinkler is required for a heat pump closet in a high-rise condo. The wardrobe is situated in a housing unit with limited access.
Ans. Yes, sprinklers are required in a high-rise condo’s heat pump closet.
According to Section 4.1.1 of the 2019 edition of NFPA 13, sprinklers must be installed in all spaces, unless specified otherwise in the standard. Section 9.2 does not cover heat pump closets, so a sprinkler is necessary.
The “closet exception” in Section 9.2.4 is limited to clothes closets, linen closets, and pantries within motel and hotel living units and does not apply to the mentioned circumstance.
#7. Closet Without a Door
Description: A four-storey hotel’s clothes closet is under 24 square feet, featuring a header but no door. Its classification for the 13R sprinkler omission exemption depends on code interpretation.
Question 7. A four-storey hotel’s clothes closet is less than 24 square feet, with a header but no door. Does this still count as a closet for the 13R sprinkler omission exemption?
Ans. Closets can qualify for the sprinkler exemption without doors, but they must fit the definition of a compartment. The clarification was included in the 2025 edition of the standard.
NFPA 13R, 2025 edition, Section 6.6.3 states that sprinklers are not required in clothes closets, linen closets, or pantries (with or without doors) in housing units that meet the following conditions:
- The total space is no more than 24 ft².
- The walls and ceiling are surfaced with noncombustible or limited-combustible materials as described by NFPA 220.
- Closets without doors must fit the criteria of a compartment (see Section 3.3.4).
According to Section 3.3.4, a compartment is a space completely enclosed by walls and a ceiling.
To open a wall to an adjoining space, the following conditions must be met:
- Openings must have a minimum lintel depth of 8 inches from the ceiling, and the total width of the openings in a single wall cannot exceed 8 feet.
- A single opening of 36 inches or less in width without a lintel is permitted if there are no other openings to adjoining spaces.
#8. How to Determine Trapeze Size When Hanging Multiple Mains
Description: NFPA 13, Section 17.1.4.1.1 states that a shared support structure must be capable of supporting five times the weight of the water-filled pipe plus 250 lbs. To size trapezes, refer to Tables 17.3.1(a) and 17.3.1(b) sequentially.
Question 8. How would you estimate the optimum trapeze size to accommodate many mains?
Ans. To support many pipes with a single trapeze hanger, add their section moduli and choose a hanger with a higher section modulus than the sum of the supported pipes.
According to the 2019 version of NFPA 13, Section A.17.3 allows for the addition of the needed or available section modulus when supporting several mains or trapeze hangers simultaneously. This section recommends scaling trapeze materials for supporting several mains, allowing for the section moduli of various pipes to be blended using the same trapeze hanger.
Consider a trapeze hanger that spans 6 feet and supports three 6-inch schedule 10 mains. Table 17.3.1(a) indicates that a 6-inch schedule 10 pipe should have a section modulus of 0.71. With three pipes, the total section modulus is determined as follows:
0.71 ×3 =2.13
Thus, the trapeze hanger must have a section modulus of 2.13 or above.
Table 17.3.1(b) suggests a trapeze hanger with a minimum modulus of 2.40, such as a 4″ x 4″ x 5/8″ angle iron or greater. Section 17.3.2 allows for the use of other materials with equal or higher section modulus.
The trapeze and its components, including fasteners and rods, must be sized to support the combined weight of the pipes.
#9. Where Does FM Global Fit into All of This?
Description: FM Global is a commercial property insurer specialising in loss prevention, including fire suppression standards. With roots dating back to the 19th century, it develops rigorous engineering guidelines to reduce fire risks.
Question 9. Not for any specific project, but curious about FM Global’s role in the fire suppression industry. What backstory do you know?
Ans. FM Global is unique in that they design their own fire protection and loss prevention standards, in addition to providing property insurance. FM Global Property Loss Prevention Data Sheets are based on research conducted at their extensive research facility in Rhode Island, which includes full-scale fire experiments. FM data sheets prioritise property damage and business operations over life safety, leading to stronger fire protection measures than normal fire codes or NFPA criteria.
Other insurance companies, such as Zurich North America, do not have the same comprehensive standards as FM Global. Insurers often follow NFPA and local fire rules, with risk engineers recommending best practices for modifications.
practices. FM Global stands out due to its dedicated research centre and large-scale testing capabilities.
FM Global is also closely associated with the NFPA. They contribute to the development of NFPA standards, such as NFPA 13, by serving on technical committees and collaborating with the Fire Protection Research Foundation.
FM Global’s fire protection regulations, particularly for high-piled storage, are sometimes more stringent than NFPA 13 and the fire code alone. FM data sheets can be a significant resource when offering alternative means and methods to local authorities, even without their involvement.
#10. Horizontal Barriers
Description: NFPA 13 (2016) Section 17.1.2.9.3 requires horizontal barriers to be 22-gauge sheet metal or 3/8-inch plywood. Specific wood constraints may include fire resistance, treatment, or material composition compliance.
Question 10. According to NFPA 13, 2016 edition, Section 17.1.2.9.3, horizontal barriers must be made of 22-gauge sheet metal or 3/8 inch plywood. Are there any special wood requirements or constraints when using plywood?
Ans. The answer is no. NFPA 13 allows the use of 3/8 inch plywood for the horizontal barrier, but does not define the type of plywood or installation criteria. The horizontal barrier traps heat and activates the in-rack sprinklers. It is not intended to function as a fire-rated separation.
#11. Suction Pipe Size
Description: According to Section 4.15.6.3.2 of the 2025 version of NFPA 20, the distance between a pump suction and a horizontally shifting elbow should be at least 10 times the size of the suction pipe.
Our vendor’s 1000 GPM fire pump has a 6-inch suction, which differs from the 8-inch suction size specified in Table 4.27(a).
Question 11. Can the requisite ’10 times’ suction diameter be predicated on 6-inch suction, despite Table 4.27(a) requiring 8-inch?
Ans. The 10 times rule applies to the suction pipe size needed by NFPA 20, not the fire pump suction flange size specified by the manufacturer.
According to NFPA 20, Section 4.16.3.3, the suction pipe within 10 pipe diameters upstream of the pump suction flange must be at least the size provided in Section 4.28. Section 4.28 mandates an 8-inch suction pipe for pumps with a flow rate of 1,000 gpm.
The suction pipe size is determined by restricting water velocity to 15 ft/sec (4.6 m/sec) to minimise turbulent flow. Turbulent movement causes air bubbles in the water, which reduces pump performance. The pump impeller imparts energy to the water, which is largely incompressible. However, the introduction of air bubbles, which are easily compressible, can induce limited areas of high pressure due to collapsed air bubbles, resulting in inefficient pump performance.
Table 4.28 note “a” states that the pump flange diameter may differ from the pipe diameter specified in the table.
For a 6-inch suction flange and 8-inch suction piping, Section 4.16.6.4 specifies an 8-inch by 6-inch eccentric reducer.
The 10 times rule measures from the fire pump suction flange to the horizontal elbow’s “flange”.
According to Section 4.16.6.3.2, elbows and tees with a centreline plane parallel to a horizontal split-case pump shaft and a distance greater than 10 times the suction pipe diameter are exempt from the requirements of 4.16.6.3.1.
When installing horizontal fittings such as elbows, tees, and crosses, ensure they are at least 10 pipe diameters away from the pump’s suction flange. Vertical fittings often do not result in unbalanced flow into the pump suction flange, although they may generate turbulence. When installing a suction fitting on a vertical plane, a long radius elbow is preferred over a short turn elbow, tee, or cross due to less turbulence. For further discussion, refer to the commentary following A.4.16.6.
Section 4.16.6.3.2 refers to the area between the pump suction input flange and the elbow or tee “flange”. The goal is to find the fitting with a minimum pipe diameter of 10 and measure to its “flange”. This could refer to the mechanical coupling on the elbow, rather than the flanged fitting itself.
#12. Definition of Intermediate Level Sprinklers
Description: The standard’s reference to intermediate-level sprinklers primarily applies to rack storage but may extend to other scenarios. A sprinkler beneath a staircase landing could be classified as intermediate-level based on placement and obstruction considerations.
Our vendor’s 1000 GPM fire pump has a 6-inch suction, which differs from the 8-inch suction size specified in Table 4.27(a).
Question 12. Is the standard’s reference to intermediate-level sprinklers limited to rack storage, or does it also apply to other situations?
Would a sprinkler installed beneath the first landing of a staircase be considered intermediate-level?
Ans. NFPA 13, 2019 version specifies intermediate-level/rack storage sprinklers as those with incorporated shields to protect from water discharge from higher elevation sprinklers (Section 3.3.205.4.8). Sprinklers are commonly utilised in in-rack storage to protect equipment from water from above.
However, they can be employed in a variety of other scenarios. A sprinkler positioned beneath a round duct wider than 4 feet may be an intermediate-level or rack-type sprinkler.
Keep it safe from water spray from ceiling-mounted sprinklers. An intermediate-level/rack-type sprinkler uses a shield to safeguard its operation element.
Sprinklers put under stair landings can be either intermediate-level/rack-type or standard. If the staircase structure naturally shields the
A conventional sprinkler may be suitable for the functioning element of the sprinkler. If the stair contains apertures, such as a grated stair, an intermediate-level/rack-type sprinkler is required to protect the operational element from water flow above.
Finally,
The complexity of fire safety regulations calls for both technical knowledge and pragmatic application. Based on NFPA policies and real-world situations, these FAQs provide a window into the daily difficulties that fire protection engineers and inspectors must overcome. From defining sprinkler needs in unusual architectural environments to grasping the subtleties of system design and inspection, every inquiry emphasises the need for accuracy and respect for accepted standards. Constant learning and adaptation are absolutely vital as the terrain of building design and fire safety changes. Professionals can guarantee the application of efficient and dependable fire protection systems by keeping current with the most recent versions of NFPA guidelines and knowing its reasoning. In the end, these revelations help to create safer homes and businesses, therefore stressing the vital need for fire safety in preserving life and property.
Courtesy: Roland Asp, CET – NFSA TechNotes – Best of February 2025